Custom Kiosk Design
Deepest Portfolio of Custom Kiosks in the Industry
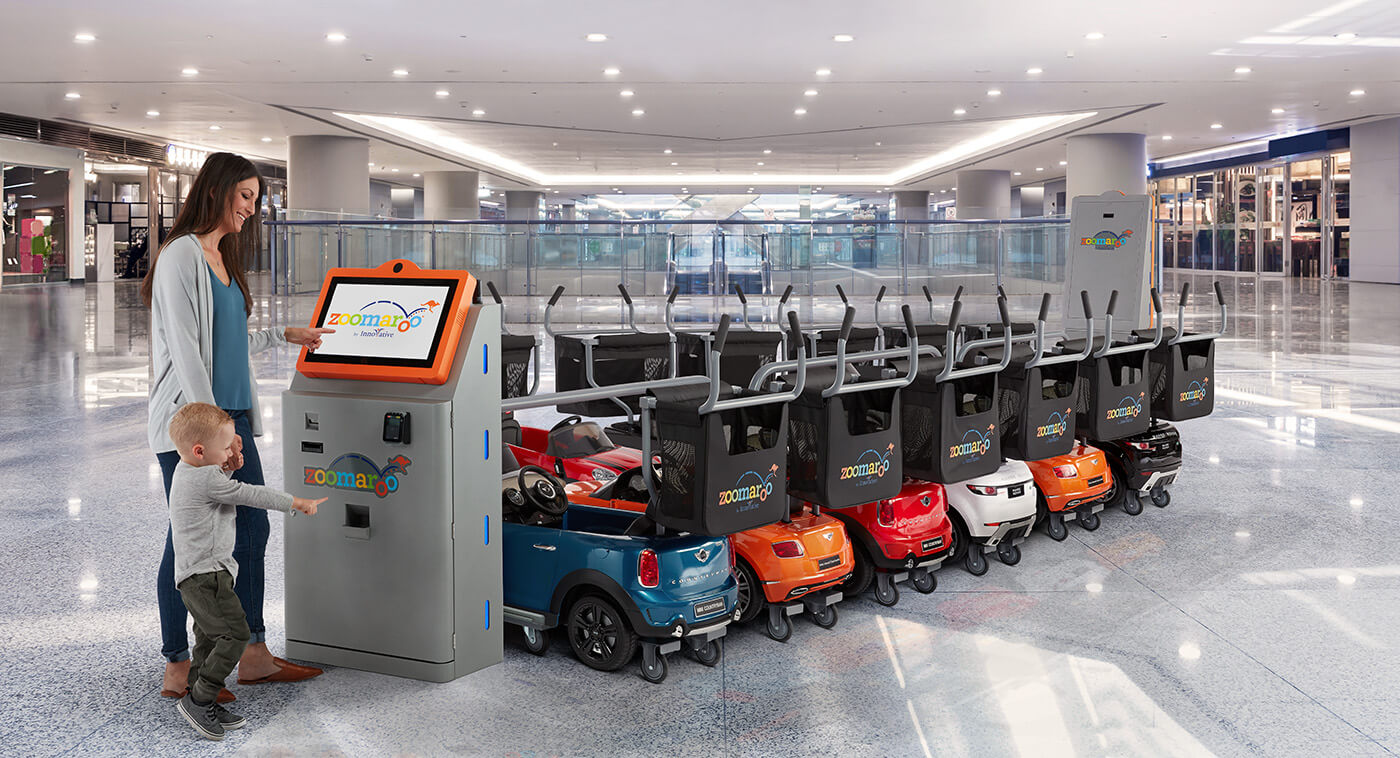
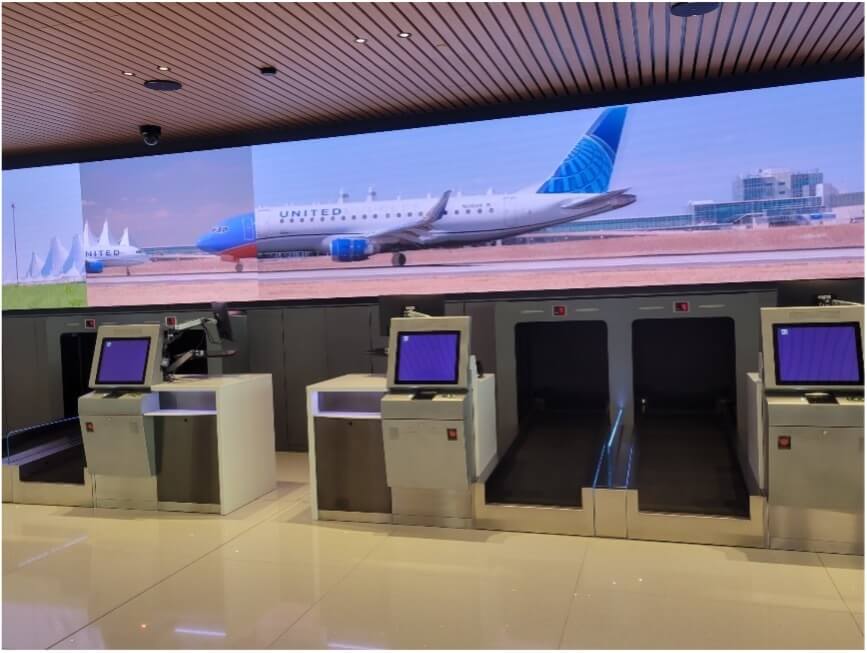
Custom Design Overview
With over 28 years dedicated to customized design and integration, KIOSK has earned the reputation as The World’s Leader in Custom Design. We have an outstanding Engineering Team including Industrial Design, Mechanical Engineers, and Safety / Compliance Engineering, who have crafted highly custom platforms for Fortune 100 clients. To accommodate the complexity of these custom projects, we’ve steadily expanded Technical Teams to surround every key project aspect with parallel Development and Project Management experts, greatly simplifying and accelerating our customer’s path to market.
Custom Design Considerations
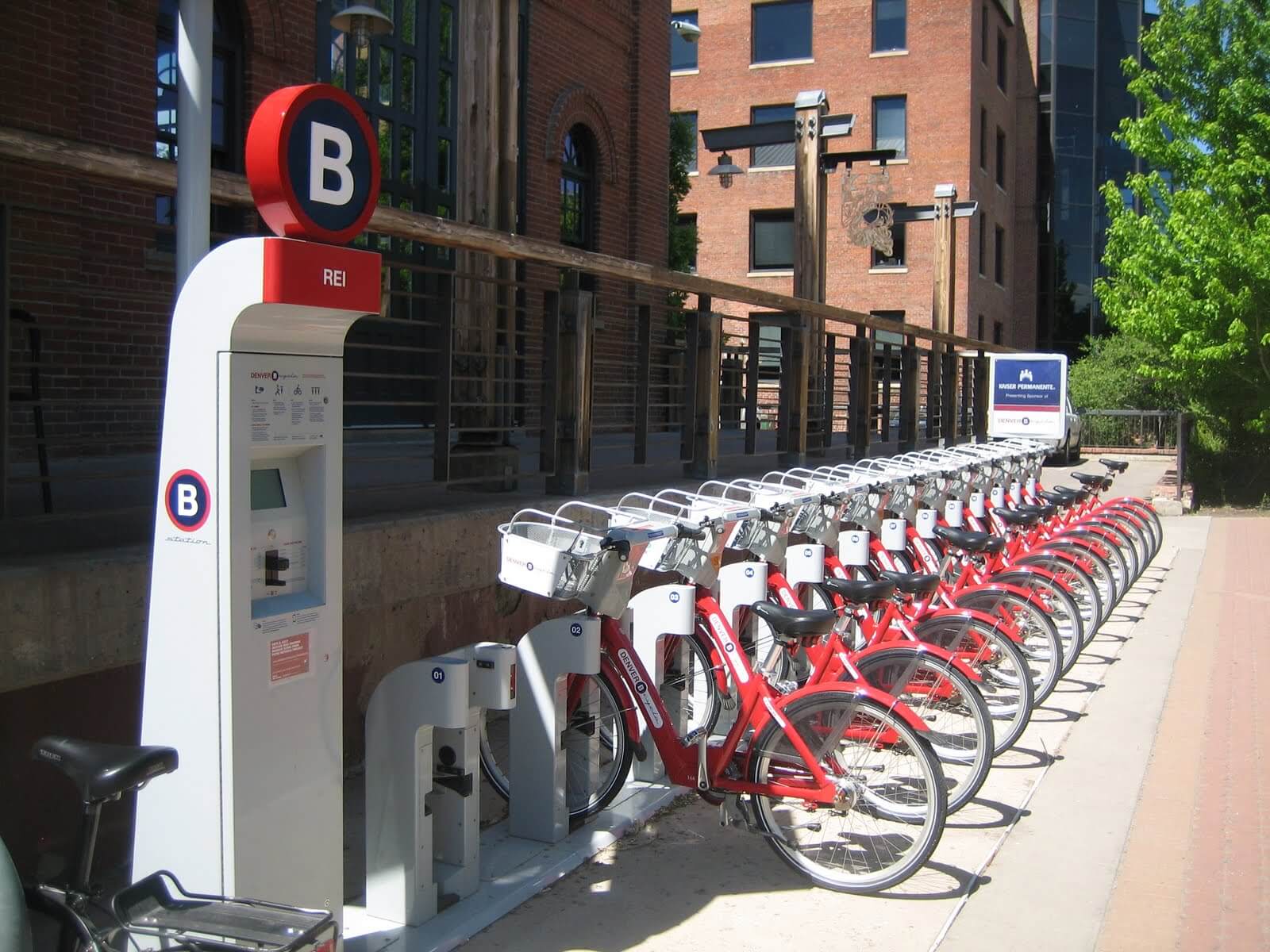
Design Experience
For over 28 years, our capabilities have been exercised and proven across 17+ vertical markets, building an unparalleled experience base for our customers to tap into.
The unique appeal of working with KIOSK for kiosk designing is two-fold:
- Agile and unrestrained solution design, completely eliminating “One Size Fits All” constraints.
- “A-Game” Team Members orchestrating all project development tracks – with the unique benefit of being together under one roof:
Solution Teams Include:
- Custom enclosure and software design
- Expert integration and in-house manufacturing
- Advanced Program Management over product life cycle
- Remote Management and field support
While most clients have general kiosk design ideas and preferences, there is no need to know how to design a kiosk. KIOSK professionals will consult with you on how to build your own kiosk elements into a design that meets your aesthetic and functional needs. Further, we can recommend components and features that help you meet the intended custom kiosk functionality and price range for hardware and related support services. In short, we’ll make it easy for your company to hit your custom mark.
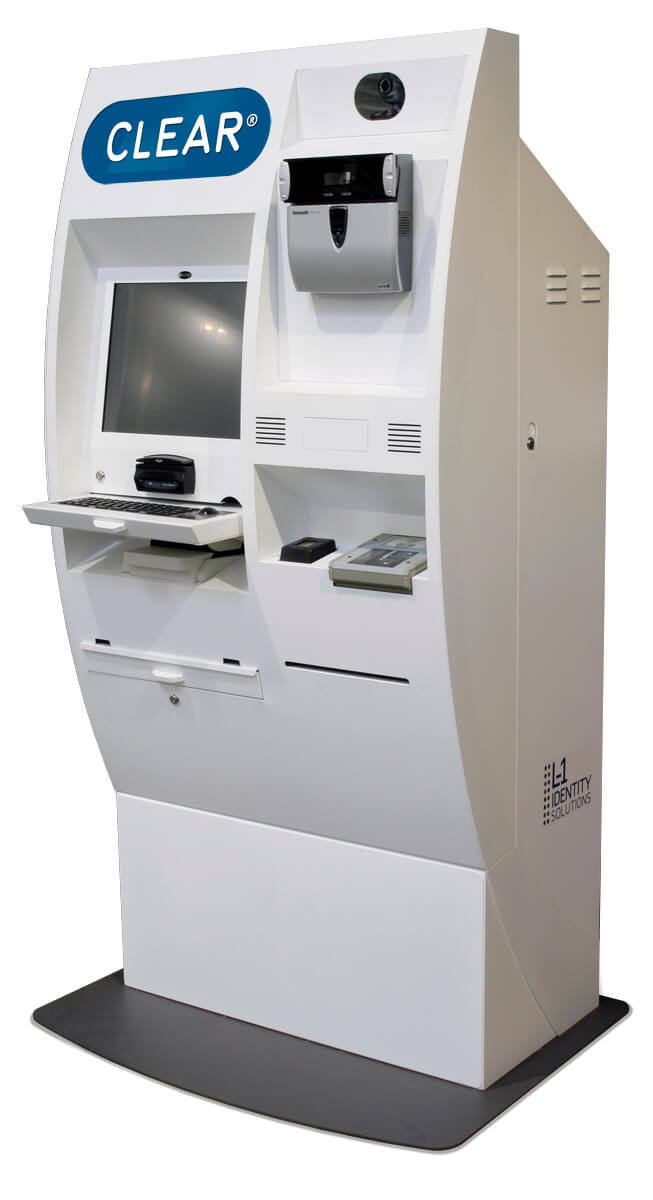
Custom Component Integration
KIOSK can accommodate component-heavy transaction requirements
KIOSK’s dominant market share in custom design ties directly to our proven ability to integrate virtually any combination of the latest self-service component technology (indoor and outdoor).
We’re the manufacturer for client solutions in multifunction financial services, airport security, and rental platforms – commonly requiring integration of 15 – 20+ distinct peripherals. More typically, KIOSK serves clients needing a “somewhat custom” creative design, with just a few unique accessories or components economically integrated into a standard style kiosk.
Integration capabilities include:
- Extensive Biometric components including facial recognition and thermal sensing cameras, iris / fingerprint / palm vein scanning
- Document scanning including passports and visas, drivers licenses, checks, etc.
- Receipt, ticket, card, laser, and photo printing capability
- Currency acceptors, dispensers, and recyclers (cash and coin)
- Wi-fi, Bluetooth / Infrared, RFID Contactless
- HVAC and Solar components for outdoor and off-grid solutions
This is simply a sampling of custom component integrations. If you don’t see it listed, just ask – most anything is possible.
How to Design a Kiosk
- 1. Design Criteria Conception
Begin with client consultations guided by KIOSK’s Engineering Process Document to establish comprehensive design criteria. This includes budget, schedule, component needs, installation, and expandability. The resulting Design Requirements Document evolves throughout the project, addressing all design issues up front based on extensive prior experience.
- 2. Component Evaluation & Modeling
Procure components as per the Design Requirements Document, ensuring compatibility with customer-specific software. Clients review and approve component specifications before KIOSK begins initial layout modeling within the overall kiosk enclosure.
- 3. Component Evaluation & Modeling
After component approval, KIOSK develops initial concept renderings to verify component placement and achieve the desired aesthetics. This iterative process involves close collaboration between KIOSK’s engineering team and the client’s project team, offering multiple creative options designed for manufacturability and reliability.
- 4. Mechanical Design & Review
Advance to a complete set of mechanical drawings. Conduct a design review to ensure all requirements are met and generate a checklist of required changes. Finalize the design based on customer feedback, ensuring compliance with guidelines.
- 5. Agency Certification/Prototype Build
Perform a “dry fit” test of the prototype components within the enclosure. Following approval, complete painting, artwork, and final assembly for first article production. KIOSK’s Compliance Engineers conduct in-house UL and FCC testing to accelerate time to market, handling all prototype development phases internally.
- 6. Installation & Deployment
Post-prototype delivery, utilizes KIOSK’s 115,000 square feet of manufacturing space for in-house fabrication and production, accommodating small runs to large volumes. KIOSK provides comprehensive field and managed services for seamless deployment, ensuring expert attention at all production scales.